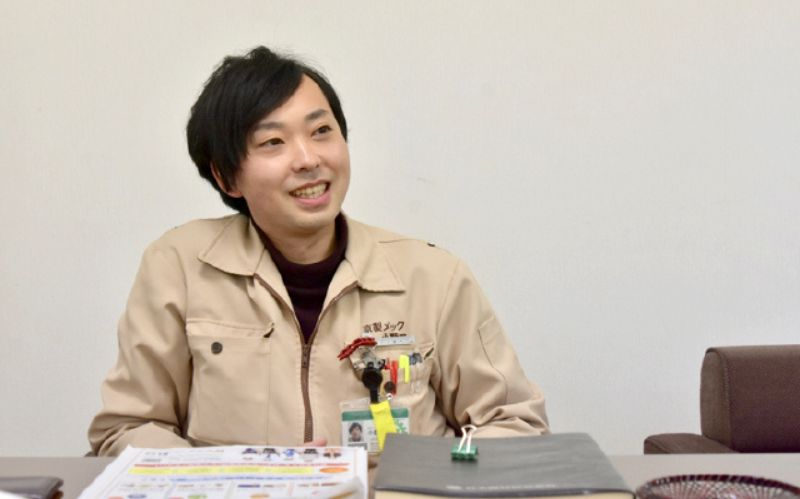
地元・大分で、日本の製造業を支える世界にたった1台の機械づくりができるのはココだけ!
地元・大分で、日本の製造業を支える世界にたった1台の機械づくりができるのはココだけ!
このストーリーのポイント
- 京製メックは大分で唯一無二の存在だった
- 一つの機械の一から十までを一人の技術者が担当する環境
- 「縦型カートナー」のスペシャリストを目指す
- インターンシップで仕事の楽しさを体感してほしい
入社してすでに約50台の機械を開発している小野。そのいずれもが日本を代表するような大手メーカーの工場で活躍している。「地元・大分で働きたい」という思いと、「一から機械づくりをしたい」という思い。それを両立できる唯一の会社として京製メックを選んだことを心から良かったと感じ、地元の後輩たちにも同じ喜びを味わってほしいと願っている。
株式会社京製メック
小野 豊
技術部 機械設計
2017年4月入社
大分大学 大学院 機械・エネルギー工学専攻 機械コース
学生時代はブレーキノイズの研究のかたわら、音楽活動にも傾倒。ジャンク品のエフェクターを修理・改造して、新しいギターでビンテージ感のあるサウンドを生み出すなど、機械いじりを得意としていた。何より地元「大分」を心から愛し、京製メックに入社。いまも休日などに地元の友達とワイワイやることが何よりの楽しみだという。
大好きな地元で、大好きな機械づくりをしたかった
大分生まれの大分育ちで、そのまま大分大学に進学。大学院では振動工学を専攻し、ブレーキノイズのメカニズムを研究していました。簡単にいうと自動車などでブレーキを踏んだ際になぜ振動が起こるのかを解析し、抑制対策を考えるという感じです。そのアプローチ法の一つを計算上で実証し、実機実験でも実現するなど、かなりの成果をあげました。
課外活動では2つの軽音サークルに所属しながら学外のバンドにも参加するなど、音楽に熱中していました。ベースやギターの演奏もしていましたが、それよりもアンプやエフェクターなどの機械をいじって音質を追求することに夢中でしたね。ネジや塗装の材質によって音が変わるのが面白かったんです。リサイクルショップでジャンク品を買ってきては、それを自分で修理・改造して理想の音に近づける。特に新しい楽器でビンテージ感のある音色を出すことにハマっていました。学業でも趣味でも、とにかく機械を触ることが好きでしたね。
就職にあたっては「大分を離れたくない」という思いと、「最先端の機械を一から自分でつくりたい」という思いの間で葛藤がありました。地元にも機械メーカーがないわけではありませんが、そうした企業には例えば「自動車の一部の開発・設計」のような仕事しかない印象でした。東京や愛知などに出れば大きな仕事もありましたが、それでも大分で働きたいという気持ちが強かったんです。
大分では京製メックが唯一無二の存在でした
実は学部3年のときに大学院進学か就職かを決めかねていて、一時期就職活動をしていました。その時に地元での合同説明会で京製メックのブースにも立ち寄っていたんです。製造現場で使われる産業機械をオーダーメイドで開発・製造している会社で、ブースで出会った社員さんもみんな温かくアットホームな雰囲気。そんな印象を受けました。
最終的には研究を続けたいという気持ちのほうが強く、就職せずに大学院に進みましたが、修了を前に「大分で就職するか、やりがいのある仕事を求めて東京や愛知へ出るか」で悩んだとき、真っ先に頭に浮かんだのが京製メックでした。そしてあらためて会社のことを詳しく知り、「ここなら大分にいながら、面白い仕事ができる!」と確信したんです。
京製メックは食品や医薬品などを化粧箱に包装する「カートナー」や、段ボールの製函・商品の充填・封緘までを自動で行う「ケーサー」といった機械のメーカーで、納入先には日本を代表するメーカーの名前がずらりと並びます。お菓子や飲料・加工品などの大手メーカー、医薬品や化粧品などの有名企業、自動車、ゲーム機、日用品など、CMで見かけるような会社ばかりです。しかも、すべてがオーダーメイドで同じ機械は二つとしてない、一つの機械を一人の担当技術者が一からつくり上げるというんです。「こんな会社、大分では他にない!」と思いました。結局、他の企業を一社も受けることなく、京製メックへの入社を決めました。
ただいま製薬会社の「縦型カートナー」と格闘中
入社後は約半年の全体研修の後、グループ会社の京都製作所で約2年の現場研修がありました。そこの研修で電気設計、機械設計、組立・調整などすべての工程を経験したことが、いまの機械設計の仕事にも大きく役立っています。「一つの機械を一人の技術者が一からつくる」といっても、すべてを一人で完結することはできません。いろんな部署の技術者と、時には意見をぶつけ合いないながら、時には協力しあって完成させていきます。だから他の部署の仕事を理解することがとても重要で、それができているからこそ抜群のチームワークが成立しているんだと思います。
京都製作所での研修から大分に戻った僕は、機械設計の配属となりました。機械設計は機械の仕組みや機構を考える部署で、仕事はまさに機械づくりそのものという感じです。その中でまず驚いたのが、京製メックでは「カム」をほとんど使わないということです。通常、機械づくりではモーターの回転運動をカムによって上下運動に変換したりして、モーター1個で様々な動きを生み出します。しかし京製メックでは、いくつものサーボモーターを使い、一つひとつの動きを個別に制御しているんです。カムを使うと、それぞれの動きのスピードなどを調整するのが困難ですが、サーボモーターなら微調整も可能ですし、様々な状況にフレキシブルに対応することもできます。機械としてより複雑で高価になりますが、そこが大手メーカーから高い評価と厚い信頼を得ている秘密であり、機械設計の仕事がより面白くなる要因の一つだと思います。
また「同じ機械は二つとしてない」のは事実ですが、機械には「型番」と呼ばれる系統みたいなものがあります。同じような機能が求められる機械では、この「型番」から改造を行います。ただし同じ系統であっても、どんな大きさ・形状・重さの商品を箱詰めするのか、どんな温度・湿度の環境で使われるのか、設置するのがどのくらいの面積で、どれほどのスピードが求められるのかなどにより、細かなカスタマイズが必要。ほぼ「一からつくる」のと変わりありません。僕はここで入社してから49台の機械をつくりました。もちろん「型番」のカスタマイズ案件もありましたが、どういうわけか型番にないような機械を任されることが多いんです。
そしてちょうど50台目となるのが、いま開発中の「縦型カートナー」ですが、これも型番のない完全オリジナルの機械です。カートナーとは商品を6個や8個など決まった数量ずつ集積して箱に詰める機械で、商品を横からスライドさせるように箱に入れる「横型」と、商品を持ち上げて上から箱に収める「縦型」があります。横型はスピードは速いけど箱のフタを閉めるのが難しい、縦型は箱を組み立てるのは簡単だけど商品を集めて揃える集積が難しいという特徴を持っています。
いま開発しているのは大手製薬会社で使われる縦型カートナーですが、一つの機械で「ジャー(軟膏などの容器)」「ポンプ(シャンプーなどのポンプ機能付のボトル)」「オーバル(目薬などの楕円形の容器)」の3種類に対応することが求められています。容器の形状が異なれば当然、それを入れる箱の形状も違ってきます。そんな条件下で「商品を集めて整える」→「それを持ち上げで上から箱に充填する」→「箱に封緘ラベルを貼る」→「レーザーマーカーで製造年月日などを印刷する」という工程を、1分間に60個という速さで実現しないといけません。しかもレイアウトに制限があり、付帯するユニットも一緒につくる必要がある…。通常、1台200時間程度でつくりあげますが、この案件は800時間を要する難易度の高い開発です。でも決して「うわ、たいへん…」と思っているわけではありません。こんな機械を任せてもらえることに喜びを感じていますし、難しい機械、ハードルが高い課題ほどワクワクします。だから楽しみながら格闘中というところです。
低コスト・短時間で仕上げてこそプロの技術者
開発中の縦型カートナーは現在、上長に相談に乗ってもらいながらDR(デザインレビュー)を重ね、ウィークポイントを一つひとつ潰している段階です。まだまだ完成には時間がかかりますが、僕が地元・大分で開発した機械が大手製薬会社の工場で活躍し、そこで包装された商品が全国のドラッグストアに並ぶ日が楽しみです。
京製メックでは、どんな仕組みで機械を動かすか、どんな機構を用いるかがすべて個々の技術者に任されています。それぞれアプローチ方法が違うので、まったく同じオーダーでも作り手によってまったく違う機械になります。そこが機械設計のいちばんの楽しさですが、決して好きな機械を好きなようにつくればいいというわけではありません。いい仕組みや新しい機構を思いついたら、そこからどれだけ部品を減らせるか、トラブルが起こらないようにするかなどを考えます。低コストかつ短時間で、いかに安定性の高い機械をつくるかがプロとしての腕の見せ所なんです。先輩がつくった機械を見ていると、「こんな簡単な仕組みで、こんな動きを生み出せるのか!」と驚くことも少なくありません。そんなときは自分にはまだ経験値が足りない、職人の勘みたいなものが備わっていないと痛感します。
もちろん僕もできるだけ多くの経験を積み、早くプロの技術者になりたいと思っています。その第一歩としてまず、社内で「縦型カートナーのことなら小野に聞け」といわれるような存在を目指しています。いま開発中の型番のない機械は、社内では「特殊機械」と呼ばれています。縦型の開発自体が少ない上に、前例のない「特殊」な機械ですから自分のオリジナリティを発揮できる場面がとにかく豊富。僕は仕事としてはコレがいちばん面白いと思っています。そんな中で自分独自の仕組みや機構を生み出し、「縦型のスペシャリスト」になることが当面の目標です。その経験とノウハウを持って、将来はケーサーなど他の機械にも挑戦したいと思っています。京製メックは「やりたい」と手を挙げた社員には、高い確率でチャンスをくれる会社ですから、成長できそうな仕事があれば、これからも積極的に手を挙げていくつもりです。
母校・大分大学のロボコン優勝が刺激に
グループの京都製作所では毎年、「キャチロボバトルコンテスト」というロボコンを開催しています。これは大会名の通り、「キャッチ=掴む」という動きに特化した技術を競う大会。年毎にテーマは変わりますが、お菓子やカップ麺など、実際に市販されている有名メーカーの商品を掴み、箱やトレーに収めるというのが基本的なルール。2010年のスタートからすでに12回を数えますが、参加チームも増え続け、優勝賞金が50万円もでて、最近は関西や大分のテレビで放送されたりもしています。
僕は数年前からこの「キャチロボバトルコンテスト」の審判を務めていますが、今年めちゃくちゃ嬉しいことがありました。なんと母校である大分大学が、京都大学や東京工業大学といった強豪を抑え、初優勝したんです。後日、大分放送でも大会の様子が放映されることになっていて、それも楽しみにしています。今年の大会テーマは「Catch the じゃがりこ!」。おなじみのスナック菓子の筒状の容器を掴み、穴の空いたケースに速く正確に収めていくという戦いでした。これまで目立った成績を上げたことのない大分大学が参加51チームの中を次々に勝ち上がり、決勝はお互いがパーフェクトスコアを出すという大接戦。延長戦の末、見事に勝利を収めたときには思わず拳を握っていました。このロボコンでは毎年、楽しそうにロボット作りに取り組んで技術を競い合う学生の姿に刺激をもらっていましたが、今年はまた格別。操作の巧みさに頼らない安定感のあるロボットをつくりあげた後輩たちの姿に感動しました。そして先輩として恥ずかしくないように、僕ももっと成長していきたいという思いを新たにしました。
こうした学生対象のロボコン開催のほか、京製メックでは月に1度、インターンシップも行っています。会社説明や工場見学だけでなく、CADで図面を作成し、それを実際に製作するという工程も体験できます。前回は板金部品で社名ロゴが入ったマッチ箱をつくり、全員が完成品をお土産として嬉しそうに持って帰ってくれました。会社はちょっと不便な場所ですが、「杵築駅」から車での送迎もあります。僕も設計担当として説明役をしていますので、これから技術者を目指すみなさんと会えるのを楽しみにしています。
また、コロナ禍でも業績が好調で2023年の春には、いまの工場の横に新工場も完成します。クリーンルームを持つ最新の設備で、「できること」がさらに増えていきそうです。ここ「大分」から僕と一緒に日本全国へ、そして世界へ、世界にたった1台の機械をぜひ発信していきましょう!